Floating Offshore Wind Turbines (FOWT) mooring systems
The decision about choosing the correct mooring ropes and systems has a significant impact on the costs of installations of Floating Offshore Wind Turbine projects and the performance of the system itself.
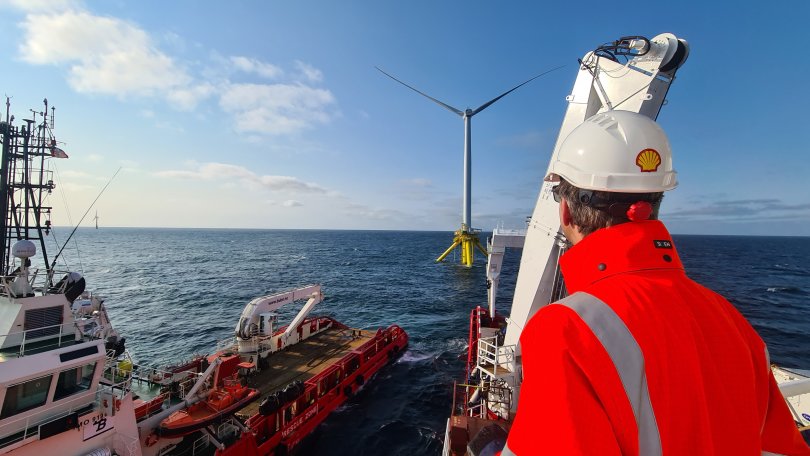
In the past, the floating offshore wind projects have used heavy and expensive steel chains for mooring systems.
Today, the engineers are looking to replace these chains with synthetic fibres such as high modulus polyethylene fibre (HMPE), for some parts, or in some cases for all of the mooring systems.
The engineering methods have been developed for determining the bending lifetime, fatigue lifetime, creep characteristics, and system holding capacity for offshore mooring applications.
DM20 lightweight mooring solutions
DM20, the low creep Dyneema® fibre is successfully used in several mooring systems, mooring of Midwater Arches, Riser Tether systems as Hold Down and Hold Back Tethers, some of them having a sophisticated redundancy system. The low creep behavior of DM20 allows the design of reliable and light mooring systems. The design life of this type of moorings is typically between 20-25 years. The same fibres were also tested in MODU (Mobile Offshore Drilling Unit) mooring systems and shown to be the most cost-effective solution where the system requires reinstallation up to several times. There is a huge benefit of using the Dyneema® due to the low diameter and lower weight which means easier handling.
DM20 – a permanent mooring component
The ultra-low creep performance of this fibre will benefit wind energy projects and the FOWT industry.
DM20 has great fatigue resistance, hence the mooring systems designs are light and efficient due to the limited material required.
The above cuts the cost of installation and contributes to the operational cost savings by reducing the need for engaging the largest anchor handlers and eases the handling of the mooring on the platform deck.
On the one hand, the lightweight of Dyneema® allows for low mooring pre-tension, on the other hand, provides sufficient horizontal restoring force.
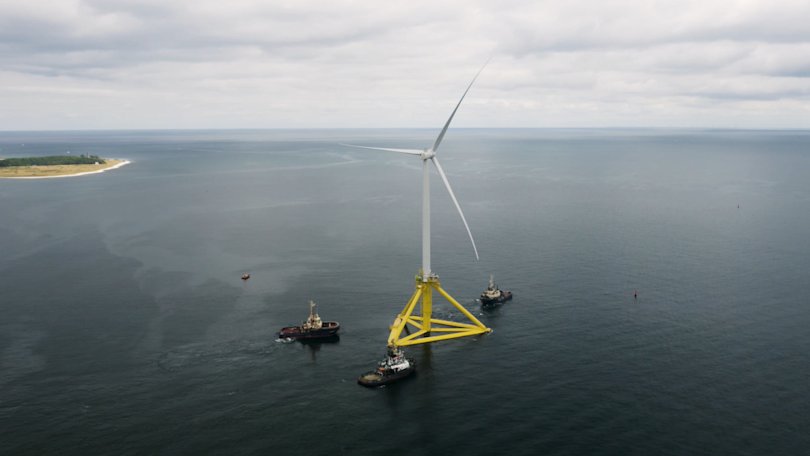
Mooring of FOWT platforms
Several demonstration projects of newly developed Floating Offshore Wind Turbine platforms have been installed and are in the process of being tested. The common concept is to have low building and installation cost. These concepts are benefitting from lightweight and stiff mooring lines with Dyneema®DM20.
FOWT mooring rope design
Dynamica Ropes offer the proven multicore parallel rope design for mooring applications :
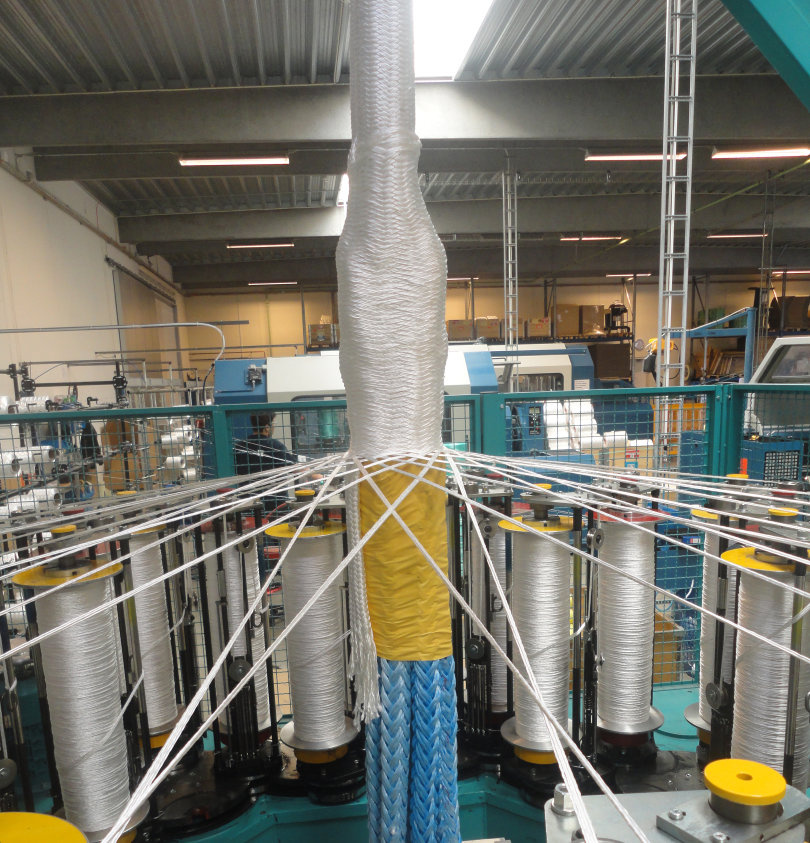
The HMPE ropes have only limited constructional elongation. The load-bearing yarn of several sub ropes mooring rope is the low creep DM20.
Dyneema mooring lines don’t need to be pre-stretched, as they have very little elongation in use
The core construction consists of several sub-ropes depending on the required strength. The sub-ropes are often protected by a mud and sand filter layer and always finished with a heavy-duty HMPE jacket. This jacket provides outstanding abrasion protection. The compacted jacket layer assures a reduction of the risk of damage during installation and operation.
Dynamica in FOWT mooring
The following points should be reviewed in the design of the mooring system:
- The Breaking Strength of the rope (based on actual testing)
- Rope splice qualification (fatigue performance)
- Creep lifetime Safety Factor over design life (based on creep rupture)
- Tension fatigue
- Static and dynamic stiffness
- Length accuracy
- Elongation during installation process
- Risk of damage during installation
- Marine growth
The above topics must be addressed through calculations and certification based on fibre properties and based on system validation. The system has to be certified in order to verify the design and testing performance.
Installation benefits of Dynamica mooring lines
The design of Dynamica mooring lines is done with ropes heat stretched during the production process, so only a limited pretension during installation and hook-up is required. Heat stretching is necessary in order to eliminate the elongation that is present in the rope during machine braiding and to take out the surplus of elongation that is in the rope due to the construction itself. The lighter weight of synthetic fibres makes them easier to handle and install than steel, and allows the use of smaller anchors and smaller installation vessels with lower running costs.
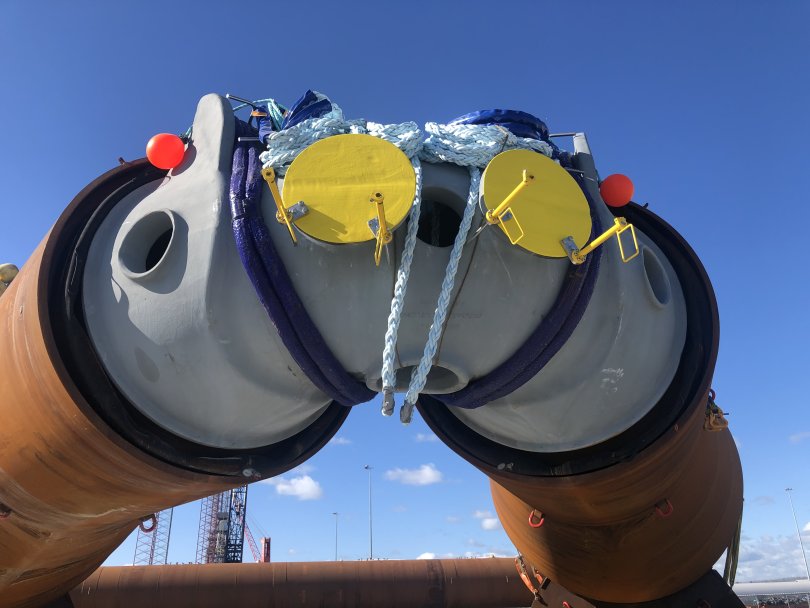
The smaller diameter requirements of moorings made with DM20 synthetic fibres means that smaller and lighter connectors can be used; hence the handling gets faster and easier.
The Floating Wind Turbines deep water mooring
The floating offshore wind turbines move into deeper waters and at the same time presented to higher winds - This means that costs for mooring and installation are a big part of the overall project budget. Designers of the Floating Offshore Wind Turbine concepts are looking for a new mooring methodology to reduce costs, minimize installation time and reduce health and safety risks seen during offshore operations.
High installation costs and the cost of anchoring are delaying the commercialization of the development of FOWT. The mooring of offshore wind platforms is a critical success factor in the future of floating offshore wind.
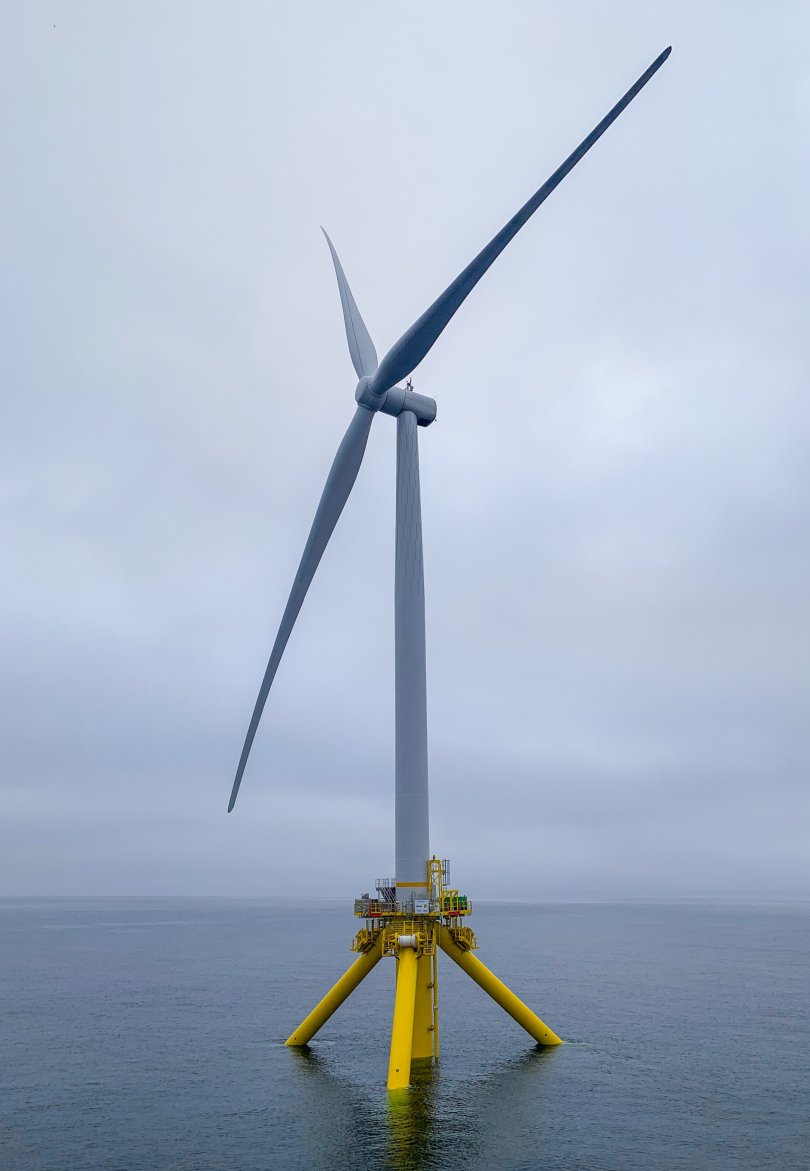
Read more about our products, services, cases and get to know us better – this way you can choose us as your trusted supplier and partner with ease.